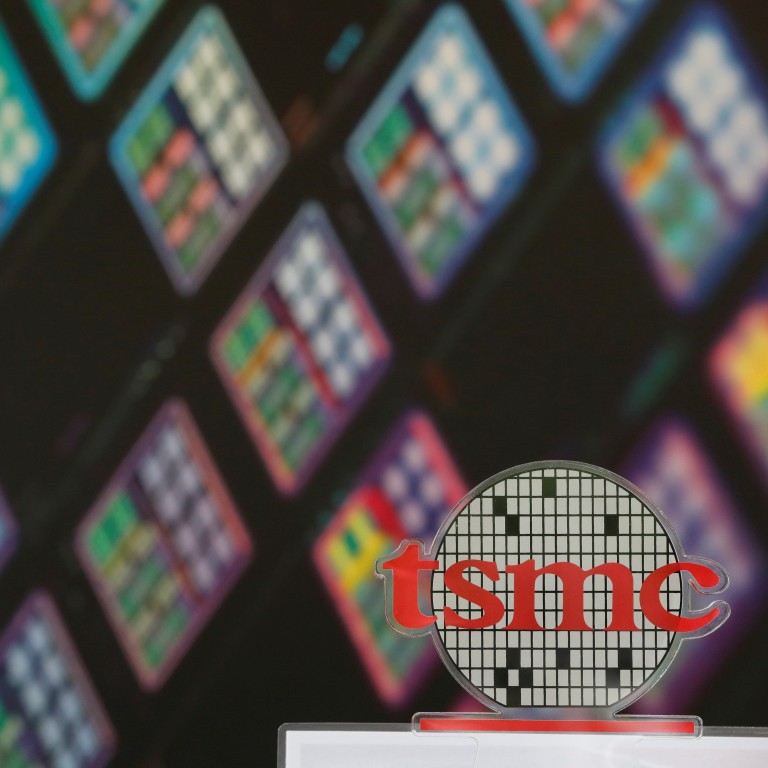
How Covid-19 changes the geopolitics of semiconductor supply chains
- Just one company in Taiwan – TSMC – accounted for nearly half of the world’s contract chip making market share in 2019
- The Japan earthquake and tsunami in 2011 led to a rearrangement of global auto manufacturing chains
US Secretary of State Mike Pompeo said the deal “bolsters US national security at a time when China is trying to dominate cutting-edge tech and control critical industries”.
On the same day, it was reported that TSMC had stopped taking new orders from Huawei, the world’s second largest smartphone company, to fully comply with the latest export control regulation imposed by the US.
These are significant shifts in the semiconductor industry. Why are they happening now?
As one of the most specialised high-value supply chains, the semiconductor industry is characterised by several bottlenecks. It is among the most globally integrated supply chain, yet is highly vulnerable.
Samsung takes another step in US$116 billion plan to take on TSMC
Devoted to the principle of comparative advantage in the pursuit of efficiency, this industry had forsaken resilience. As a result, this lean and agile supply chain made itself vulnerable not just to a global risk event such as Covid-19 but also to export controls such as the ones directed against Huawei. The events of the past six months are likely to force a re-evaluation of this trade-off towards building more redundancy.
Specifically, the semiconductor supply chain is susceptible to four risks.
The first is concentration risk. Semiconductor companies have a significant concentration of their manufacturing or service bases in a single country. For instance, Japanese vendors have a quasi-monopoly for certain chemicals necessary for chip production – roughly 70 per cent of etching gas and 90 per cent of photoresists for the world market are produced by Japanese companies.
Similarly, just one company in Taiwan – TSMC – accounted for nearly half of the world’s contract chip making market share in 2019. Many large electronics vendors such as Apple or Huawei rely on the Taiwanese company to manufacture chips for their latest generation of smartphones, laptops and other gadgets.
If the production in any of these choke points halts because of Covid-19 or other disruptions, repercussions will be felt not just in the semiconductor industry but in many other sectors that rely on semiconductors – from cars and medical equipment to renewable energy power plants and on down to smart home gadgets.
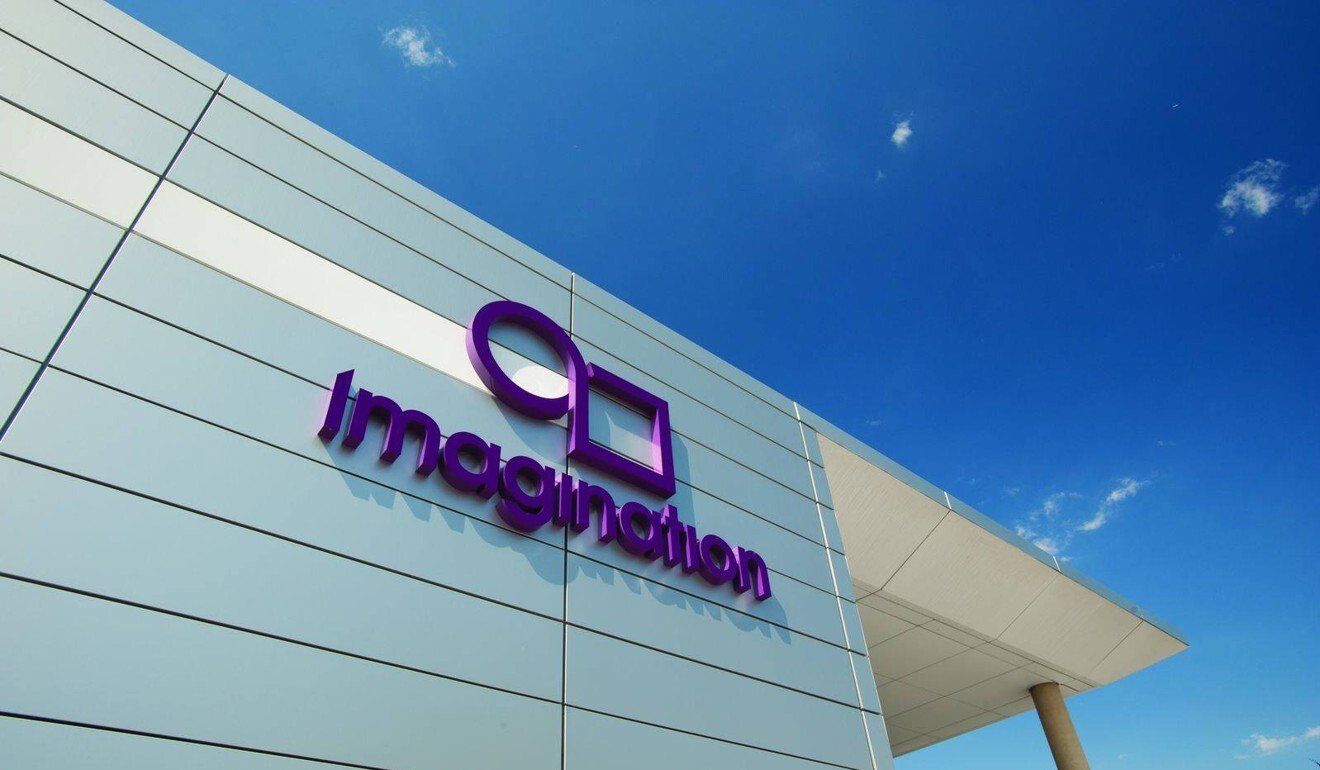
The second risk is overspecialisation. Because of the huge capital investment required, semiconductor companies are highly specialised in a few geographic locations. For example, memory chips, a key component of every smartphone, laptop or server, are being produced by essentially three companies. Samsung and SK Hynix in South Korea and Micron Technology in the US together hold roughly 97 per cent of the DRAM world market. Overspecialisation again forces interdependence. The supply chain works seamlessly at most times until there are climatic or geopolitical stressors that expose the absence of redundancy.
The third risk is to business continuity. For several narrowly defined markets in the semiconductor manufacturing process, there is just one dominant player. For example, the Dutch company ASML is the sole producer of a special type of manufacturing equipment necessary for producing leading-edge chips.
The largest chip making plants in the world, Samsung and TSMC, rely on this one company. If those shipments get delayed, either due to Covid-19 or trade restrictions, production road maps across the supply chain take a hit. Ensuring business continuity becomes increasingly hard in a global, highly concentrated and specialised value chain.
Chips are down for China, as American firm shuts semiconductor factory
The final risk is a geopolitical one. The economics of semiconductor supply chains – turbocharged by efficient and lean global supply chains – have made it a viable geopolitical tool. William Shih of HBS elegantly describes the semiconductor industry as “a transcontinental relay race with hidden hurdles”. And nation-states can place these hurdles in the path of competitors. This, in one line, is the summary of the ongoing trade and technology war between the US and China.
To be sure, semiconductor supply chains were non-resilient even before Covid-19. The structural geopolitical tensions between the US and China meant that both governments and private companies were starting to question their own over-reliance on a handful of technology vendors. But it did not make “business” sense then as building resilience needed heavy capital investment to bring down the bottom line.
But Covid-19 has exposed these gaps like never before and will force a rethink of policies in the following respects:
First, the semiconductor industry will be seen in even more strategic terms than before. In the US the Semiconductor Industry Association (SIA) petitioned President Trump to allow continuity of operations on the grounds that it is “essential infrastructure”.
In the past, the US gave huge subsidies to prevent the mass exit of producers from the DRAM market in the face of Japanese competition. China is following that playbook even more aggressively today. Going ahead, governments will apply technology transfer requirements, investment restrictions, and tax breaks with greater fervour to the semiconductor industry.
Japan recently created an economic stimulus package to encourage a shift of manufacturers out of China. Such packages could be used by other countries to build a more resilient semiconductor supply chain as well.
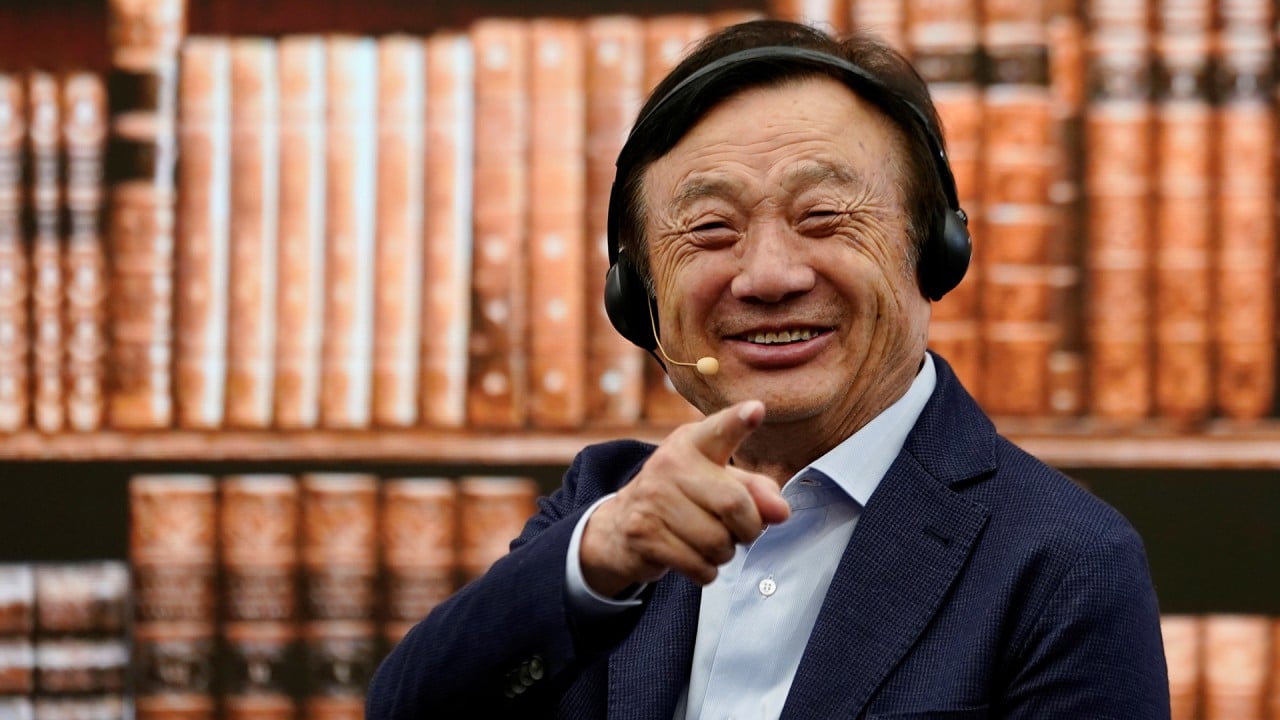
08:55
Huawei's founder on US sanctions, 5G leadership and building trust in Europe
Meanwhile, in Europe, an attempt to change control of the board of British semiconductor IP company Imagination Technologies by an investor linked to the Chinese party-state was stalled by the UK government. Such instances will become more commonplace as the ongoing economic crisis will hurt more companies in the coming months.
Finally, the extent of diversification for resilience will vary across the supply chain. Given that there will be a crunch of capital investment globally, setting up new chip fabrication units – requiring billions of dollars of upfront capital investment – is less likely. It might need multi-country consortiums, swayed by arguments of economic nationalism, to take the plunge. On the other hand, setting up fabless companies – relying on excellent human talent and research expenditure – is far more likely.
The Japan earthquake and tsunami in 2011 led to a rearrangement of global auto manufacturing chains. Companies changed their sourcing and manufacturing as Fukushima prefecture was responsible for 60 per cent of critical auto parts for the global market. Covid-19, an event of a much larger scale, will similarly change the resilience-efficiency trade-off in the semiconductor industry. National governments and the geopolitical environment will be the key drivers of this transformation.
Pranay Kotasthane is the Head of Research at Takshashila Institution, a centre for research and education in public policy. He leads a project on the geopolitics of semiconductors.
Jan-Peter Kleinhans is a project director at Stiftung Neue Verantwortung (SNV), a charitable, non-party and independent tech-policy think tank in Berlin. He is leading SNV’s work on ‘Geopolitics of Technology’.
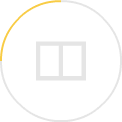