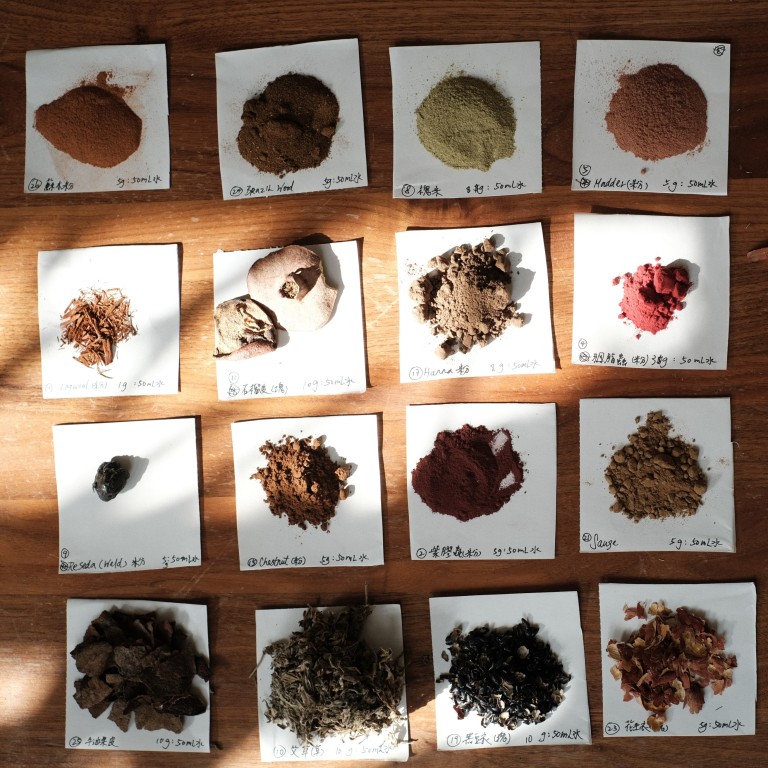
Fish skin leather, onion peel dyes: sustainable fashion designers from Hong Kong put their own spin on traditional crafts
- Kinyan Lam specialises in natural dyes, working with hues tapped from the skins of foods such as onions, pomegranates and black turtle beans
- Noelle Lee is breathing new life into the old craft of fish-skin leather, which is light, thin and stronger by weight than many other types of leather, she says
People love avocados for their creamy and nutritious green flesh. But Kinyan Lam sees them in a different light.
He’s drawn to the fruit’s tough and rough skin that, when boiled, can produce varied shades of pink.
Lam is a Hong Kong-based fashion designer who runs his eponymous label, as well as Genau Studio in Sai Kung, which specialises in natural dyes.
And some might be surprised by Mother Nature’s vast palette: Lam works with 440 tones of natural dyes, including hues tapped from the skins of foods such as onions, pomegranates and black turtle beans that are commonly used in Latin American dishes such as black bean soup and gallo pinto (rice and beans).
Fashion rental store that takes aim at clothing waste ‘just really good’
“People assume that natural colours are dull or grey but that is not the case,” says Lam via video call from Paris, where he was showing a collection at the recent fashion week.
The glitzy event in the French capital, a magnet for top designers and A-list celebrities, is a far cry from his childhood spent on a small farm in China’s Guangdong province, surrounded by lychee and mango trees.
“I grew up among mountains, trees and animals, which inspired my love for natural dyes,” says the 29-year-old, who relocated to Hong Kong with his family aged 14. “It’s why I have a strong emotional attachment to plants and natural materials.”
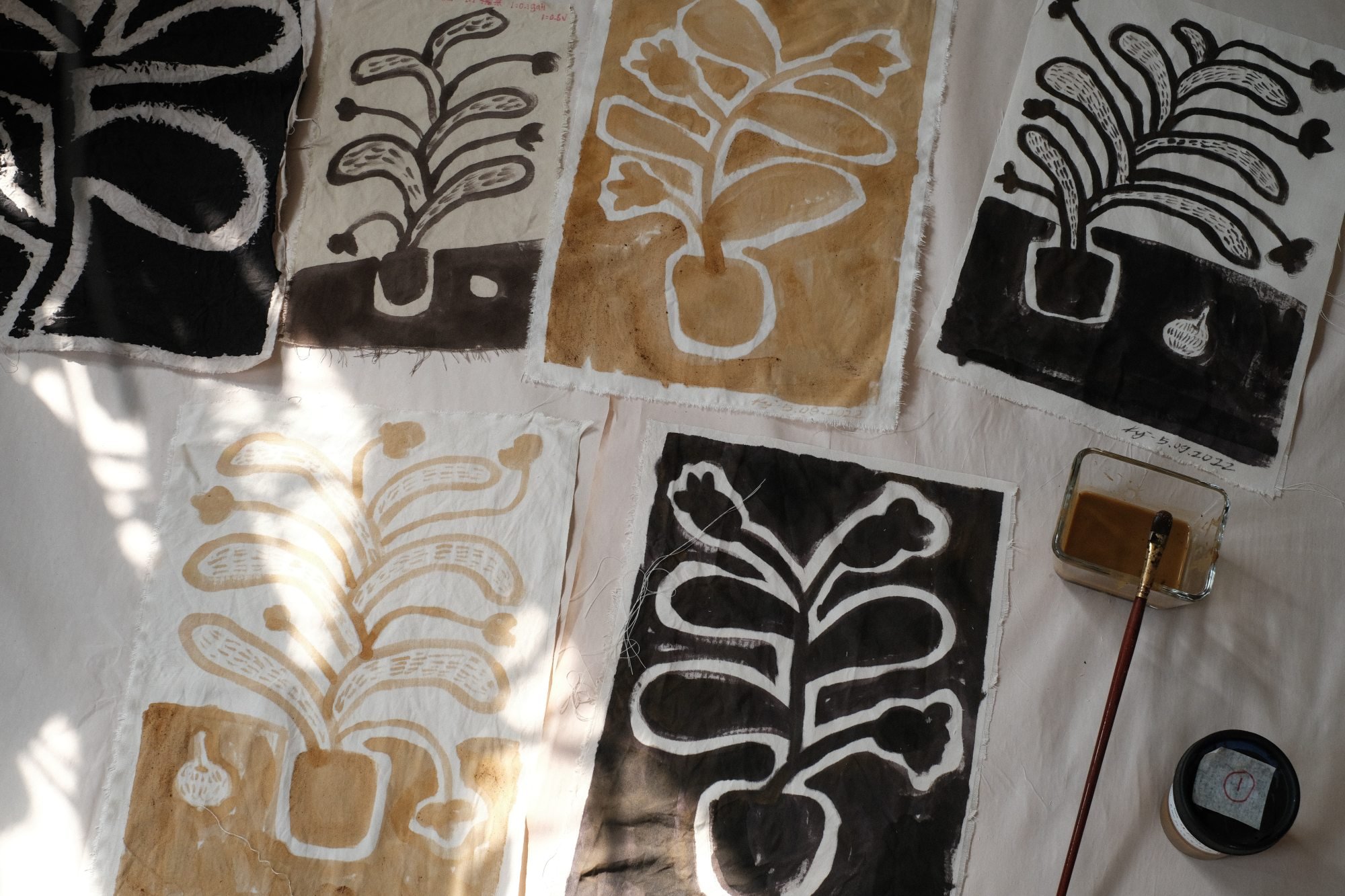
A graduate of the London College of Fashion, Lam says a career in fashion never blipped his radar while he was a child running around in the countryside wearing clothes passed down from his cousin. He received new items only at Lunar New Year.
“Back then I knew nothing about fashion,” he says.
Today it’s not just his sharp, carefully crafted designs that are wowing audiences but his drive to raise the profile of artisans in the south of China.
His first collection, launched in 2020, was inspired by the traditional handmade fabric sustainably produced by the Dong community in China’s Guizhou province.
“I visited there to see the traditional ways of spinning yarn, dyeing fabric, weaving and embroidery,” he says. “It was an awe-inspiring experience.”
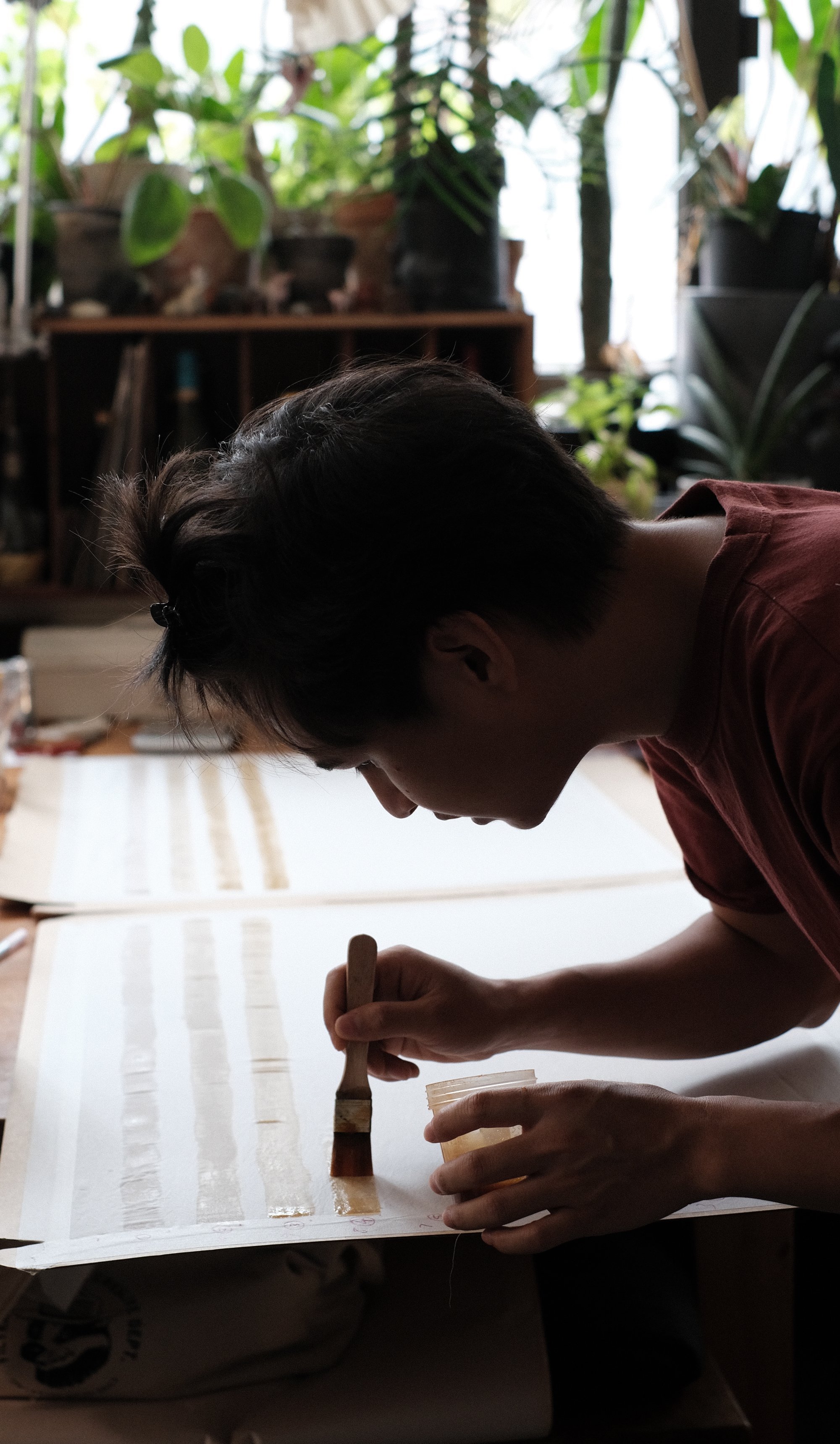
Hongkonger Noelle Lee loves a creative challenge. At the moment she’s making a set of wearable wings for a play in Vancouver, Canada, where she’s been based since finishing university in 2020.
What makes the assignment unusual is that she’s constructing them out of salmon-skin leather, which she also made.
Lee, 26, is part of a movement of designers breathing new life into an old craft – fish-skin leather has been around for centuries, having been used by indigenous peoples until machine-made fabrics took over.
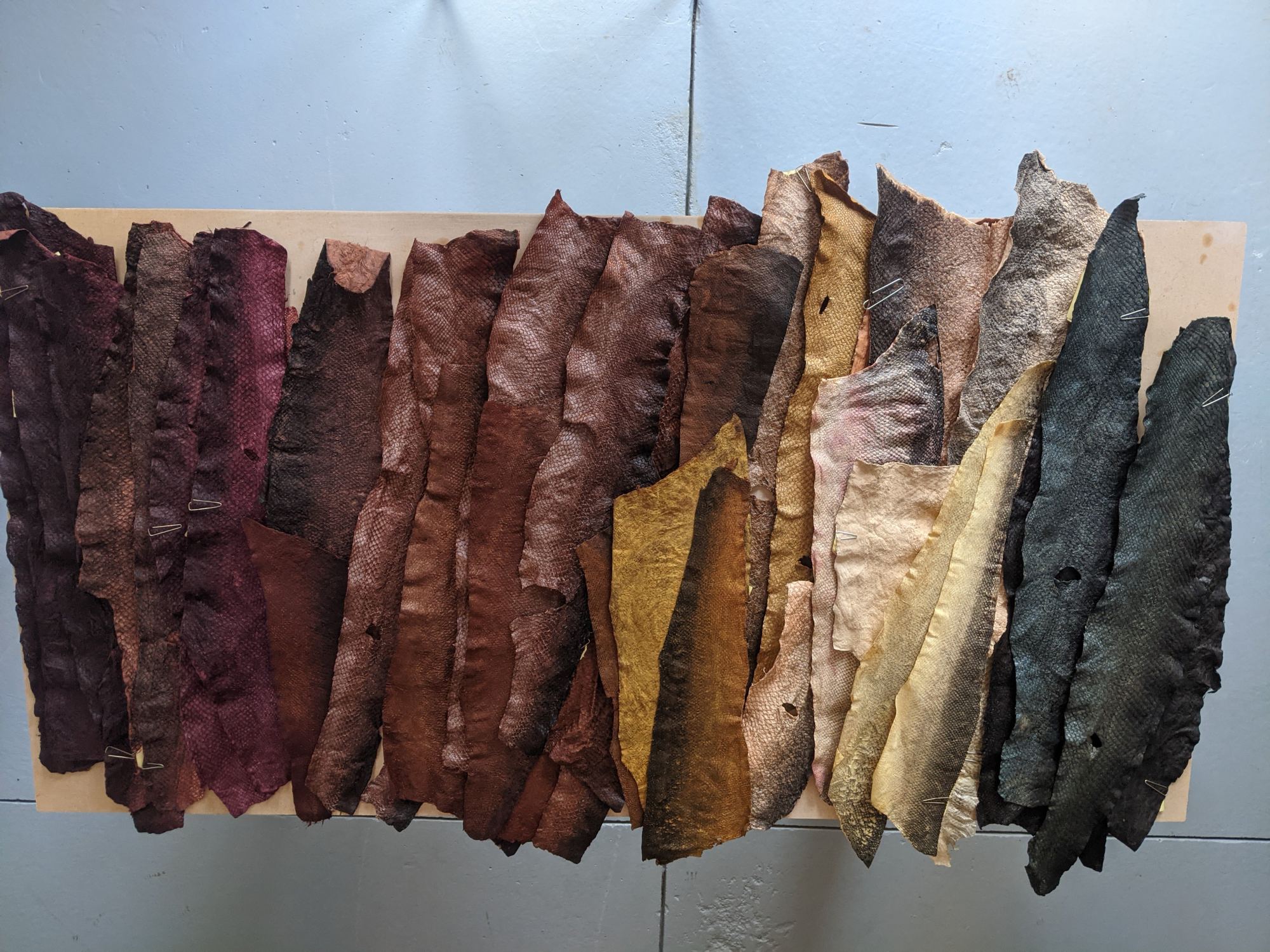
“The process in each culture differs slightly but involves the same way of chemically restructuring the skin in order to preserve it for a longer period of time,” says Lee via video call from Vancouver.
The finished leather looks a bit like snakeskin, says Lee, and is light, thin and stronger by weight than many other types of leather. “That’s because the fibre structure in fish leather runs crosswise instead of parallel like those in cowhide or pigskin.”
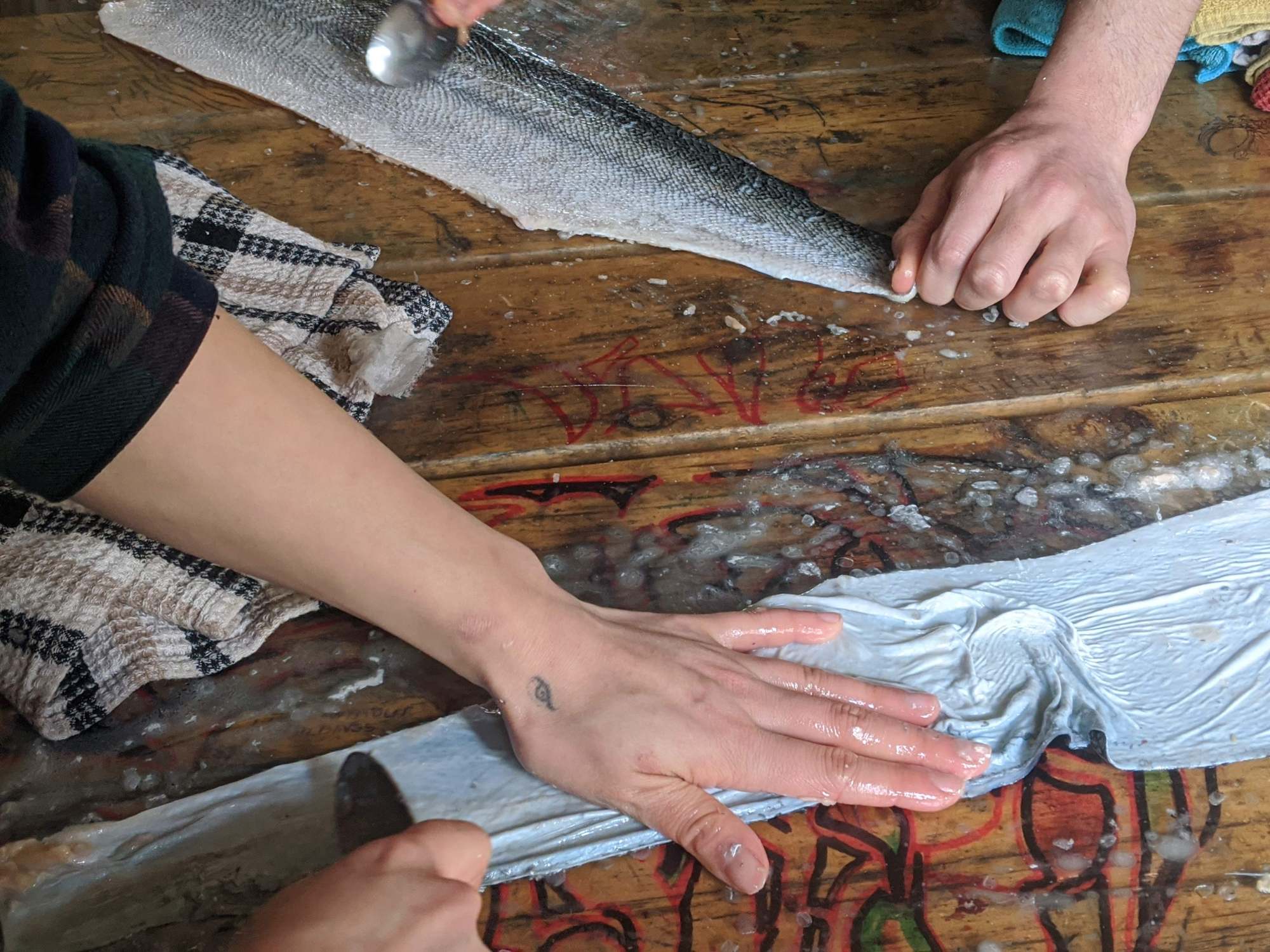
Lee has been taught by a mix of mentors with different backgrounds, including Canadian-Japanese, Canadian-Chinese, local Canadians and Scandinavians.
She also did her own research, describing Fish Leather Tanning and Sewing (2012), by Swedish writer Lotta Rahme, as incredibly helpful. “I recommend it to anyone who wants to learn,” she says.
As for the process, Lee says that when a fish dies, it starts to degrade pretty much immediately, “so you need to get it into a freezer, or something to preserve it, as fast as possible”.
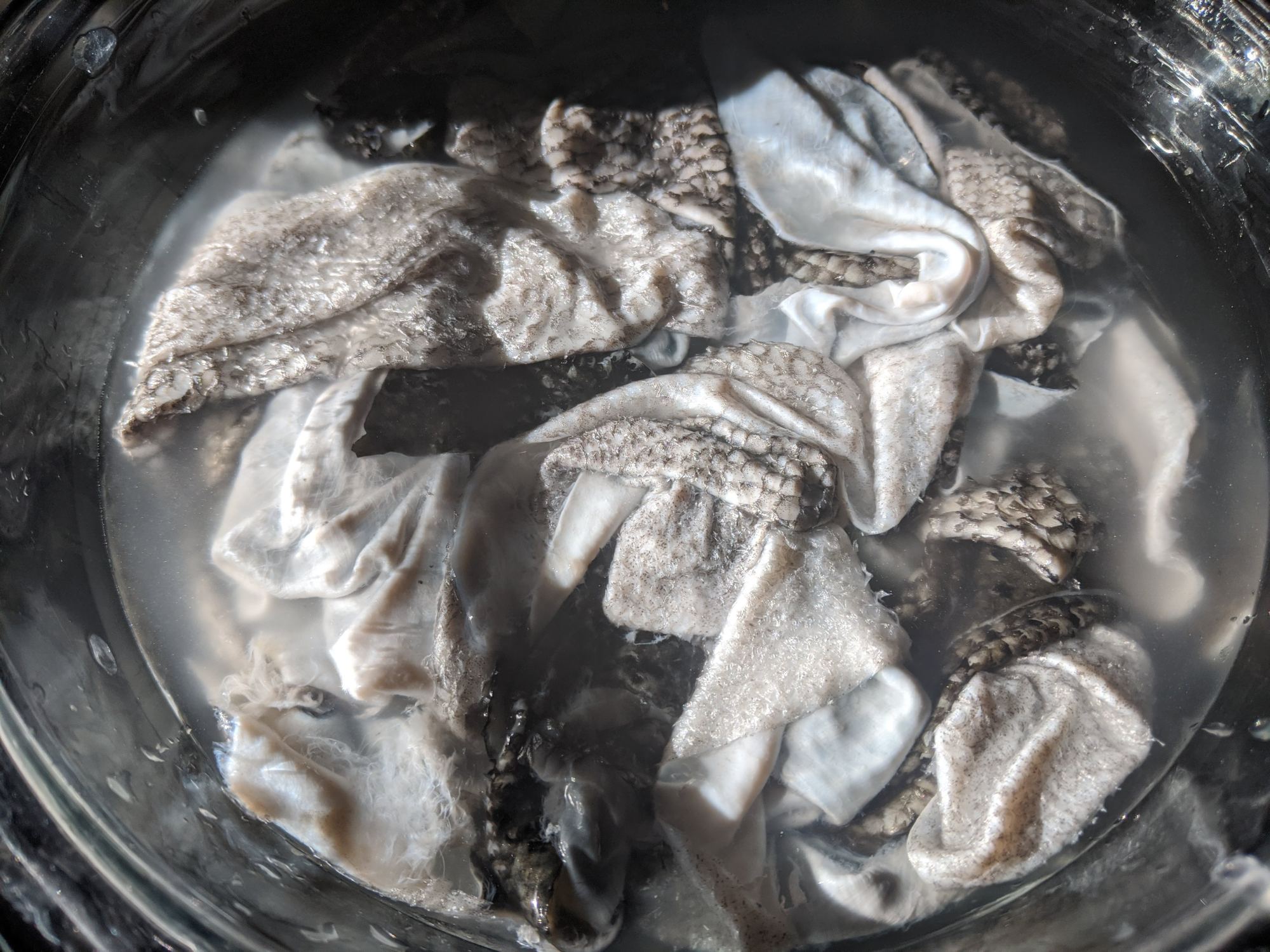
The scales and flesh are then removed and the skins immersed in tannins, the naturally occurring chemical compounds found in many plants.
“There’s a lot of tannins in specific kinds of tree bark and they are what traditionally would have been extracted but I get it in powder form.”
Skins are soaked for about 10 days – “depending on their size and the concentration of the soup” – and once bulked up with the absorbed tannins, the fishy smell disappears. They are ready within two weeks. Cowhide, on the other hand, takes months, says Lee.
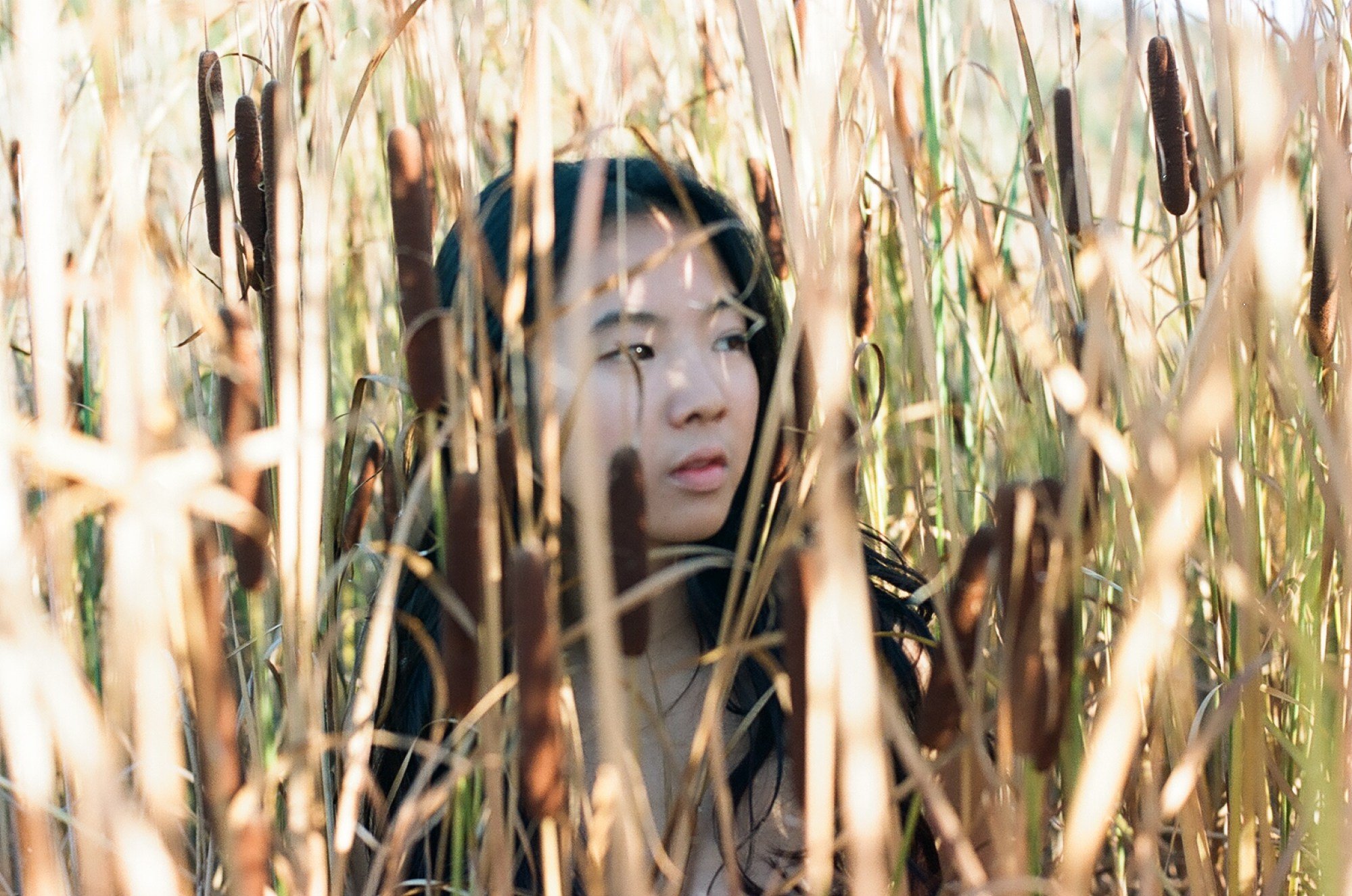
Stretching the skin is the most labour-intensive part of the process. “If you want it soft, you have to stretch it for a long time,” she says, adding the smallest skins she’s worked with were about six inches (15cm), the biggest up to 30 inches.
While big fashion brands from John Galliano to Dior have dabbled in fish-skin leather, it’s the smaller boutique brands that are driving the movement, lured by the material’s eco-friendly traits.
Fish skin is a by-product of the seafood industry that often goes to waste. Using it as leather prevents it from going into landfills.
Why fixing fashion’s pollution crisis requires big brands to share the cost
But for Lee, it goes deeper than just being a sustainable fashion material.
“Some people think fashion is quite superficial, but the leather-making techniques that I’ve been taught come with specific lessons,” she says. Using every part of the fish shows respect for it.
“It’s not just the production of things, it’s what you learn from the fish, what you learn from catching the fish, what you learn from working with natural materials.
“It’s a specific relationship that you’re nurturing.”
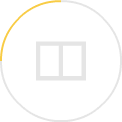